A new generation of process control system DCS viscose production line - 1.0 control system
Product model: the JTDC - DCS - 1.0 control system
Based on fully integrated automatic idea, powerful function, the fieldbus technology oriented solutions
一、Overview
According to the rapid computer technology development of industrial automation control theory, as well as the production process of the reliability of the control system, operation ability, the ability to scale, open, operating and monitoring levels, put forward more and more high demand. In this situation, JTDC DCS - 1.0 process control system, as a new generation of process control system, is developed to meet the demand of viscose manufacturing process. JTDC - Siemens DCS - 1.0 is to use the PCS 7 DCS system and S5 and S7 series hardware, on the basis of combining the most advanced electronic manufacturing technology, network communication technology, graphics and image processing technology, fieldbus technology, computer technology and advanced automatic control theory, facing the viscose process control applications and development of advanced process control system.
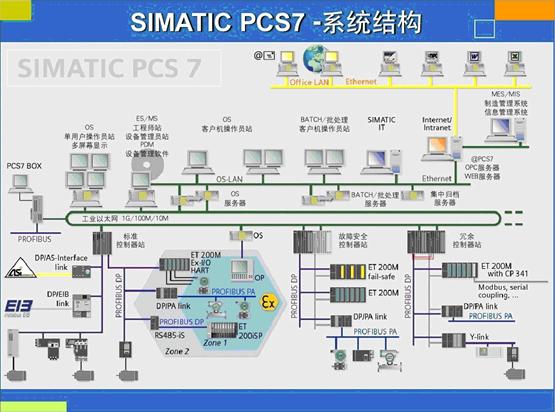
JTDC DCS - 1.0 the outstanding feature of the system are:
◆ Mixer based on fully integrated automation
◆ In pieces with the organic integration of PROFIBUS field bus
◆ Absorbed all kinds of advanced technology, for viscose production process, in line with the advanced viscose production automation production requirements
◆ More dispersed system configuration, is particularly suited to distributed process control applications
◆ System configuration is flexible, easy to extend
◆ Modular structure, common hardware modules
◆ Powerful software system, configuration and programming easy
◆ Pieces of human-machine interface products improve the level of monitoring and management
二、Monitoring and Operating
JTDC-DCS-1.0 Process control system is the window of operate station, all the operators, mangers and maintenance engineers should tracking process activities or participate in production control at a standard, friendly and process window, get the alarms and the operator indications
The connection of client and server adopted standard Ethernet. On the server, the operate system adopted Windows XP Server. On the client, the operate system adopted Windows XP Professional. On the Client and Server, the monitoring software adopted SIMATIC WinCC.
PCS7 should adopted single operate station mode, when there are many more users or the system need high requirements, should adopted Multi- Client structure. Multi- Client structure should allow a client to access the multiple servers at the same time. The operation should finish at a same time, project data、process variable、saved data、alarms and messages are obtained from the OS server of Multi-Client. So the data should distribute in a number of servers, Multi-Client access it from a public operation. A plant is divided into some technical units. Each unit has its own Os server. The advantage of distribute system is divided into several different parts, so as to improve the usability of the system.
2、Dispaly
◆ JTDC-DCS-1.0 system 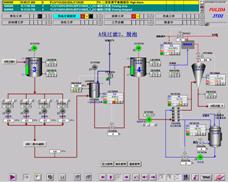
◆ Each CRT of the control system should display the characters and picture information, the operators should use a mouse through the CRT pictures to operate and monitor the producing and running.
◆Each picture should display the real time data and the state of the equipment, these data and state update at the set time. The display of the data and pictures change with the process state. The bar chart and the trend should display at any place of the picture.
◆ All the points of control system, including analog input, analog output, digital value input, digital value output, intermediate variable and calculated value, can display on the picture. For each measuring point, also shows its number, words, engineering unit, high and low limit, etc.
◆ The operator station can provide a variety of window display.
◆ Operator station software has step sequence control logic and the sequence of the simulation figure display function, the number of images is not restricted. Operating crew can complete manual control through the mouse to the picture devices. Image on the device is under a state of automatic program control, simulation shows on the drawing equipment and automatic program is the latest state to which step. If any failure occurs in the automatic program, the alarm and display of the failure occurs at which step.
◆ Operator station software provides users with rich graphics and instrument symbol library, users can also build custom new gallery, the new library can be stored and retrieved.
◆ The performance of the operator station directly dependent on the performance of the PC hardware. Using high-performance PC will obtain high performance obviously. Picture only restricted by the hard drive capacity, the number of each picture for the process of measuring point number can reach more than 500.
◆ Operator station adopts multi-layer structure, to display the number of layers according to the technological process and operation requirements to determine, the multi-layer display can make operators easily turn pages, in order to obtain necessary details and for specific operating conditions is analyzed. Multi-layer display including general appearance (district), display and loop in groups.
3, Alarm
JTDC DCS - 1.0 system alarm signal function of the process control system to support the operator to deal with accidental events, these events are generated in the production process or not normal, do not often occur in I&C or don't want to happen, these events will be reported to the operator when happen.In addition to these events, operator intervention is also completed into the alarm concept, can be classified as to the current alarm list and files. There are three different types of alarm ranked as follows:
◆ Process incident occurred in the process of automatic alarm, such as process signal exceeds the limit
◆ I&C alarm generated by PCS 7 find and report on its own components fault. This kind of failure range from a component failure, even a disconnection alarm sensors connected.
◆ Operating variables alarm occurs in the operating process, such as when change a closed loop controller model. If you use the library provided by the operator, operating alarm will be automatically generated.
4, report (record) and storage
Operator station provides a set of integrated reporting system, a database of all process can be printed. It can be put in the input output data in the following ways, in the process of output page format is free, user-defined. In addition to print the printing paper, you can also print output to a file and print preview on the screen. You can define the print task by the hour, day, week and month report form output .Report output can be triggered in chronological order, trigger event triggers or operators.
◆ Information order records can print out input information immediately to the pre-defined printer, line by line to print
◆ Information archive can be divided into short-term and long-term archive document. Short-term archive can store up to 10000 messages, reach to 10000 archive information, the new information covering the oldest information in the first place. The continuation of long-term archive for short-term archive, is usually placed on a hard disk or floppy disk, only limited by disk space.
◆ Operator station with the help of a Wizard (the Wizard), and AS the function of the control station, can easily achieve operation record.
Based on fully integrated automation, powerful, the fieldbus technology oriented solutions
◆ Operator station can periodically or event to trigger to record the measured values through the tag manager .Users can not only record external measurements, but also record the internal label value, or from any application value and manual input values. The measured value of the data is stored on the hard disk archive, the range of sampling period between the 500 ms to one year. In order to quickly access these measurements, the system provides a circular buffer in memory to manage these data (curve) online.
◆
The operator station provides different methods to record measurements:
◇ Archive has continuous cycle, namely the boot and then stored in order to set time measurements.
◇ Cardiac cycle of selective archiving, begins to store measurements which satisfy certain conditions.
◇ Cardiac aperiodic archive, that is, one or more events trigger or stop recording measurements
◇ The archive has overruned.
5, Comprehensive open operation and monitoring system
OPC (OLE) is applied to the process control and the introduction of guarantee the operation
The openness of the monitoring system of OPC promoted the process control system, operator control and monitoring system, the interaction between field equipment and office applications.
As OLE has contributed application in the field of Windows in the office, OPC is for automation for the same job: it means that the interface problems of all the difficulties will be readily solved. OPC automation system components provide "plug and play" function.It makes the long-running debate about the interface problem in the past, but also solve the problem of the connection between the components.So, people in the application of WinCC configuration system can focus on the develop practical solutions for the current.These standardized communication interface really saves expensive Labour cost.
.gif)
6, Online observation of SFC
◆ Observe SFC (the Visualization of SFCs) :
◆ Pieces automatically generated by the engineer station run SFC configuration software configuration of the SFC
◆ Each SFC has a window
◆ Has transfer mixer with spare parts (transitions), and the overview window of steps (steps) details
◆ Choose according to the SFC's name in the list window
◆ Pieces for each transfer of dynamic conditions and steps can be showed in detail
.gif)
7、Multi VGA
Multi screen technology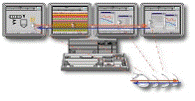
◆ An operating station can connect 1 to 4 display screen
◆ Pieces with a set of operating equipment (keyboard/mouse) to operate
◆ Pieces can be operated comfortably by storing the current
8, industrial TV online
◆ TV card + OCX
◆ Pieces from the access of the camera video images can be used as part of the HMI,
According to process images, can be used as embedded window, or as a fixed window
◆ Operators can be used to observe the scene maintenance personnel in the maintenance process
◆ Pieces to observe the specific objects in the process of production, such as flame, foam, etc.)
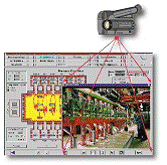
9, Redundancy option
Redundancy option can make two redundant WinCC station running at the same time, to ensure the continuous process and control operator. If a failure of the two stations, another can replace statements transmit and process the value of the archive. When the fault recovers after the operation, the site which does not work collected the all process of archives and the value message is copied to the site now resumed. Thus can be run at the same time again to two of the same station WinCC. Use this concept to configure redundancy value under the management of all process files and a message, to ensure the data integrity. In a client/server mode, the client automatically switch from fault redundancy server to redundancy with the station. After a short switching cycle, the operation of all station keeps on working. In order to simplify the configuration, can use the project replicators, it copies all the configuration data to cooperate station, and accordingly match it.
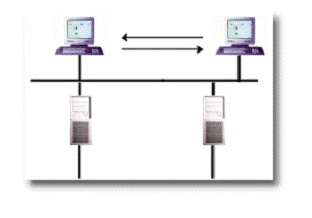
10, Perfect user Access control (Access control)
999 kinds of user permissions can be assigned permissions, up to 128 users, 10 groups.
The operator
Technology director
◆ Each operator/group mixer can set up his own access permissions
Maintenance personnel
◆ In pieces each function access can be defined separately
Pieces can be set to a unit for operation or not
◆ Can use a password or magnetic card (chip card) to set access control
◆ Protect each object (object), and each operation (operation)
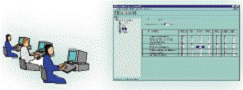
11, Time synchronization,
◆ In pieces the Central master clock (Central master clock)
◆ OS can be as the main or second-rate connect to SIMATIC NET system
◆ All pieces AS connected to the system bus, and OS periodically
◆ Mixer DCF model - or GPS clock or even to the OS (optional)
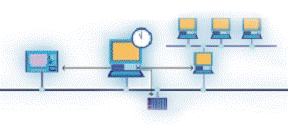
三、Engineering and configuration?
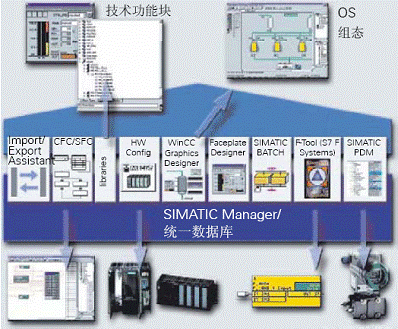
Engineer station is used for configuration on the JTDC - DCS - 1.0 system. It used the integrated global database and unified configuration tools. It just needs one configuration tool in the entire life cycle of project. The configuration tool is SIMATIC program manager which is adopted modern software architecture to manage the project, process files, archive files and build files.In project management, SIMATIC program manager has managed in two different concepts that are base on system hardware and manufacturing technique at the same time. The two concepts in the program manager are called Standard Hierarchy and Plant Hierarchy respectively. Standard Hierarchy is responsible for hardware of system such as controller, the system bus, I/O system etc. Plant Hierarchy is responsible for craft process that divided into various subsystems according to the requirement of the process in the whole factory. Actual structure of factory has adopted layered form that makes the subsystem mapped to controller. Compare with the traditional DCS-1.0 system, JTDC-DCS-1.0 system is direct to technological process.
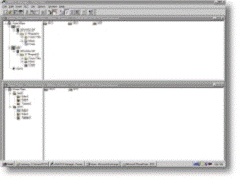
Plant Hierarchy
Standard Hierarchy
1、data base
PCS7 system has standardized, openness, powerful relational, distributed database as a platform for data acquisition, data processing, data analysis and process control management system database supporting system. Relational, distributed database platform is different from the general database supporting system, it can ensure system data integrity, consistency and the data of all parts of synchronicity, perform a variety of forms of data query, data correlation and data index. So when the system is configured, all data and settings are automatically connected to a unified database.
2、Testing and start-up support
In addition to support the system configuration, SIMATIC program manager has wided range of special function which provides support for testing and starting. These features include:
◆CFC has testing and start-up working mode, variable value in chart can be display and modify directly when it is online.
◆SFC has testing and start-up working mode. It can track the process of order functional diagram and manual intervention
◆Have a high level language named SCL
◆In the engineering system, S7 PLCSim (optional packages) can simulate automation system
◆The process signal of I/O module driver function block has signal simulation
◆ Wincc can switch mode of operation that is used for optimizing and modifying online.
3、CFC continuous control algorithm
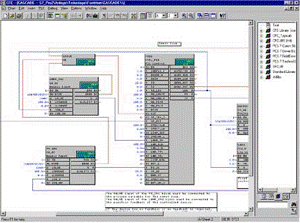
CFC is a simple graphical configuration tool, it adopted the IEC1131 standard. CFC helps to save time and cost. At the same time, greatly simplifies the system configuration and maintenance. Using CFC for configuring that is based on function block. System has layouted a lot of function block for preprogram. The function blocks are in the form of libraries. Every function block has a parameter list. Each CFC has 6 pages. The connection between the function block can be in different pages that is suitable for complex large control tasks. CFC is mainly used in configuration of automation control tasks which are continuous process.
4、The SFC sequence control algorithm
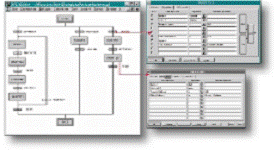
SFC is a kind of graphical configuration tool. It also adopted the IEC1131 standard. SFC is mainly used for small batch operation sequence control in automatic task. When the graphical configuration tool is configuring, it needs to draw up the sequence diagram firstly. Sequence diagram can choose sequence, parallel branches, alternate branch and loop local structure etc. In the size of two squares respectively express Step and transfer conditions (Transition).
5、Powerful databaseJTDC DCS - 1.0 system provides users with powerful, abundant library of function block, contains the common algorithm, graphic and controlscheme of certain device. At the same time, the user can also use SCL, figure language center, a graphics editor and other technology to build their function block and libraries. Engineering company or user can even generate a single function block which includes the control scheme of the whole plant, and you can refill his own name. For each function block in continuous control language has matched a corresponding graphic panel in the operator station.
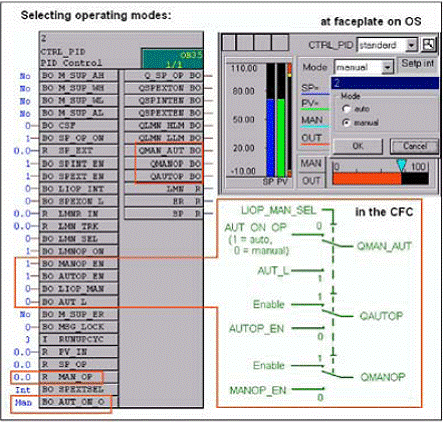
6、Configure operator station
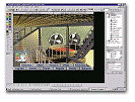
All OS dedicated configuration are used the relevant tools to complete in program manager of JTDC DCS - 1.0 system. The flow chart is established by graphics editing program. Action, documents, records and curve is done in configuration mode. Alarm function is implemented through configuration which not have to be multiple inputs, at the same time alarm function is implied in the CFC/SFC function block.
When AS links to OS, connection between the images block in AS, the alarm function block and document variable can be generated without any additional configuration.
7、Clear and concise hardware configuration
◆ Drag and drop the hardware on the frame (rack) in the appropriate position from the hardware catalog dialog window.
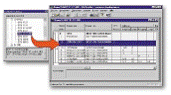
8、Concise and convenient network configuration
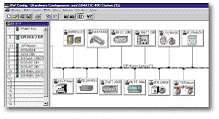
四、JTDC - DCS - 1.0 automation control system characteristics
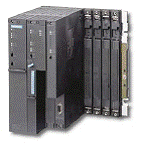
Automation control system is used for implementing the field equipment running status monitoring, data acquisition and processing, automatic closed loop control, electric equipment switch control system.
The CPU is S7417 series CPU which is designed for process control. The ground floor of the CPU chip program uses the class PASCAL language which provides the platform for CFC, SFC. Industrial controller CPU has super ability that bit operation, character operation, fixed point only needs 0.03 us, such as floating point need only 0.6 us, built-in user memory can be up to 20 MB, the maximum I/O capacity can reach 128 k switch values, 8 k analog.
1、More advanced redundancy design
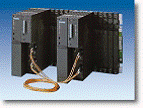
CPU-417H central controller adopts the most advanced design idea of redundancy, the redundant controller installed in a rack and installed in two separate rack that have greatly improved reliability than traditional DCS redundant systems. Main features are:
(1)Central controller in the CPU - 417 - h has preinstalled redundant software. When configuration the user can be completely ignored the redundant features, enter a user program like a redundant system configuration.
(2)Event-driven synchronization function. For performing can cause two redundant CPU after all the internal state of different orders, such as updating process image area, direct access to the I/O, interrupt and alarm, update timer, such as automatic synchronization between CPU, rather than in a particular time period to synchronize.
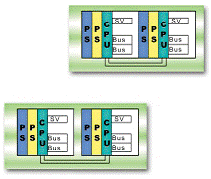
(3)Two redundant controllers can be installed on two standard rack respectively.it also can be installed on a compact rack. Compact rack uses discrete back plane bus, make the power supply, communication card and CPU still were split into two separate parts.
(4)Each redundant controller can be configured a power supply, when the demand for higher environment, can be set up for each controller two power supply. Even if it installed in a rack, because back plane bus is independent each other, still can be is equipped with two power supply in each CPU.
(5)all components can be replaced during the operation , when replace the CPU, the system can make CPU which install newly automatically updated to the current state
2、ET 200 distributed I/O
ET200 distributed I/O uses for field signal acquisition, sending the CPU's instruction to the actuator.ET200 distributed I/O type is rich, powerful, easy installation, can be good for all kinds of complex automation tasks, adapt to all kinds of bad environment.
The prominent characteristics of SIMATIC ET200 distributed I/O:
Rich species, applicable to the explosion-proof, intelligence and other different design requirements
◆Apply PROFIBUS field bus technology connect the central controller with I/O units that is greatly improve the intelligent level of the I/O parts.
◆Support hot plug, can realize maintenance, expansion or change the configuration online.
◆Less cable which saves space make the installation work greatly reduced.
◆Using fiber optic cable connection, effectively avoid the electromagnetic interference.
3、ET 200 x I/O uses for bad environment
A high degree of protection IP65, modularity, waterproof (NEMA 4 x, protection grade IP65) and unique interface design make ET 200 x a highly flexible system.
I/O modules and the integration of motor starter can combine to each station, provides a quick and optimized integration for the application of your machine or device of each control unit.Modular unit ET 200 x which works independently can directly processing control tasks on the machine. Therefore, the central controller can be free from lengthy procedure. Reaction time of the key signal has greatly accelerated. Make your ET 200 x can be used for screw conveyor, separation and filters or lift where the local intelligent control.
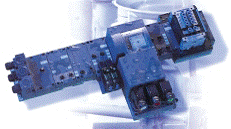
4、I/O T 200 is I/O process installed in explosion protection area
Latest used in hazardous areas ET200is distributed I/O system, it can be installed directly in the regional 1 or 2 (EEX DE ib ia/ib IIC T4).If necessary, actuators/sensors can also be installed in 0 area.ET200 is intrinsic safety type model which has modular design, thus can best adapt to application system, and ET200 is composed of a fire power, interface module used in the PROFIBUS-DP and a maximum of 32 of the electronic module, do not need to fire certification during the running of HART function and heat exchange is standard performance of ET200is module.
Combined with JTDC - DCS - 1.0 system, has the system diagnosis, time tag and CFC drive block, and other functions.ET200is start simple and conveniently; Through the SIMATIC product data management (PDM) directly configures electronic module and parametric field devices on the project site.
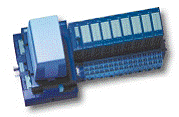
五、 JTDC DCS - 1.0 industrial automation control system communication network
JTDC DCS - 1.0 using SIMATIC NET industrial communication network structure has the rich, flexible network level and SIMATIC NET protocol in all levels of communication is in accordance with international standard network protocol that guarantee the openness of the system. All applied in SIMATIC NET products and module are specially developed for industrial applications, suitable for may suffer from serious electromagnetic interference, etching liquid, high pollution and industrial environment, mechanical shock SIMATIC NET network has been installed and used widely, through the test of time.
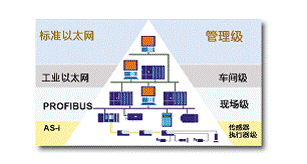